Off-site Construction Solutions for Healthcare
Modular construction can elicit different thoughts depending on the audience, as the term can describe a wide range of construction types. Are we talking about modular homes, modular headwalls, or modular cruise ships? To fully understand the differences in modular construction, it is essential to clarify the options and implications of each type.
Modular construction falls into two main categories, repeating units or customizable units. Within each of these, the level of modular construction can vary. Repeating units focus on standardization, making them easier to manufacture and assemble for greater efficiency and scalability. In healthcare, for example, modular headwalls or inpatient bathrooms can be fabricated repeatedly in an assembly line approach.
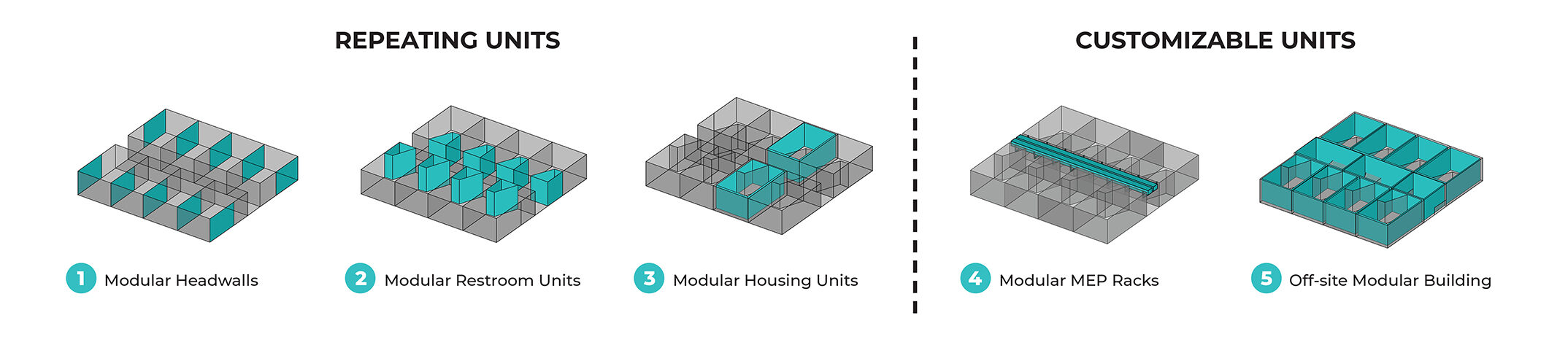
Customizable units are adaptable and can be tailored to meet specific needs of a project when repeating units either cannot be achieved or there are not enough units to take advantage of scale. For example, MEP racks can be fabricated adjacent to the site and then hoisted above ceiling when ready, decreasing installation time for major MEP infrastructure.
Off-site construction differs from other modular approaches by being fully customizable, including space planning, room complexity, and design, and by moving 75% of the construction to a factory site. Off-site construction also takes the greatest advantage of these additional benefits of modular:
1. Schedule Reductions
Off-site construction can lead to substantial construction time reductions due to the overlapping construction sequences. While site work and foundations are underway on site, the building steel and interior finishings are being constructed off-site. Weather delays are not a factor for modular off-site work, reducing possible schedule changes.
These schedule reductions generate greater flexibility without affecting the end deliverable date. And in healthcare, a shorter schedule can mean earlier income generation.
2. Quality
Construction occurs in a controlled environment which often leads to reduced material waste and higher quality control compared to on-site customization.
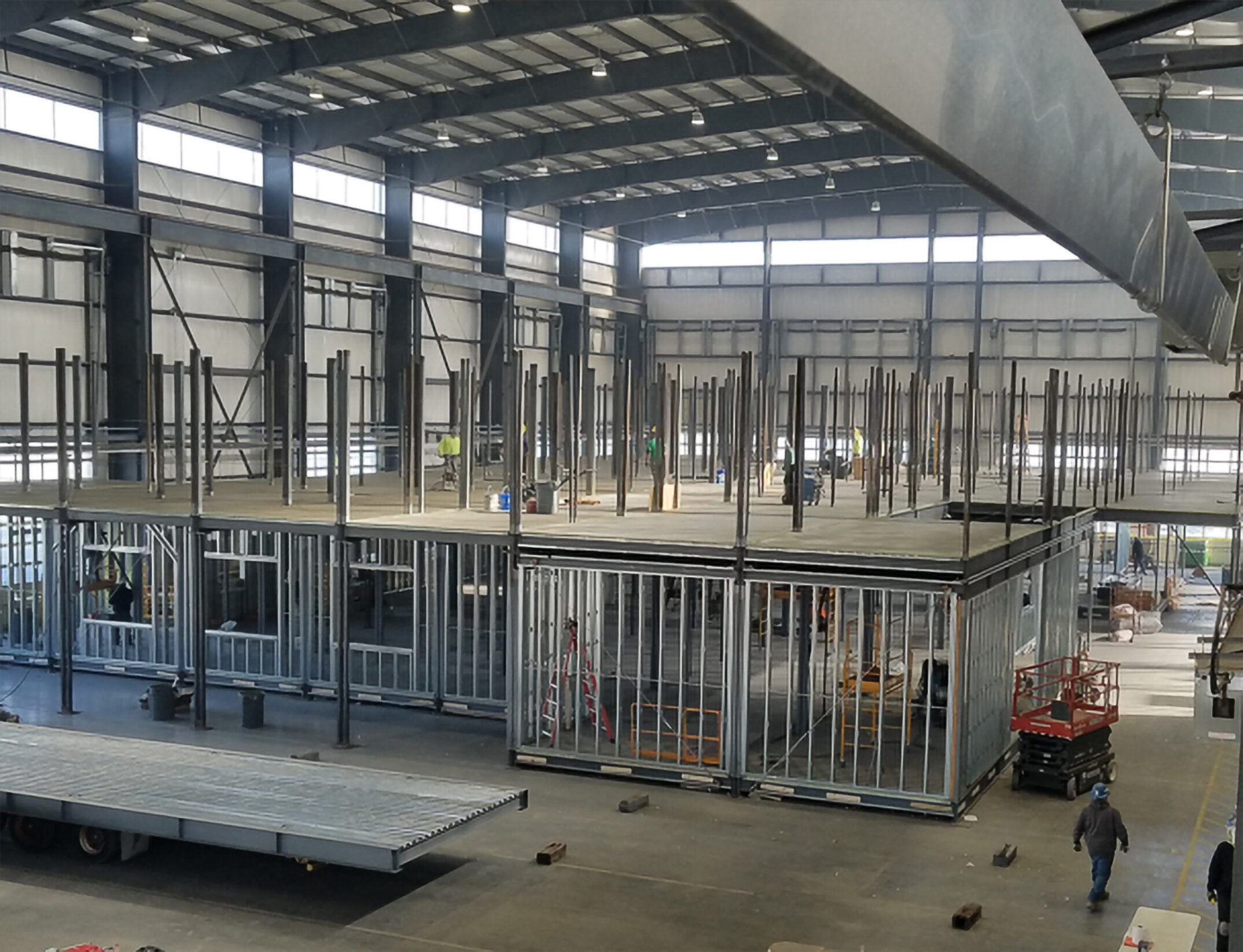
Modules under construction at a MODLOGIQ factory. Photo provided by MODLOGIQ
3. Local Labor Shortage
In communities that have a large amount of construction or a lack of skilled labor, off-site construction allows for the delivery of a high-quality building by moving the construction to a location that has a dedicated labor force.
4. Site Logistics
Moving most construction off-site reduces the impact on the building site, including the required footprint, overall project time, and site lay-down space, as work shifts to a controlled environment. Healthcare facilities have complex flows, from emergency departments, supply drop off areas, and patient circulation. Minimizing on site time and space disruptions improves patient satisfaction by reducing interruptions to those flows.
5. Flexible Design
Offsite construction is not limited to repeating units to gain efficiency. The layout in each module can be unique since the building is fully fabricated together in the warehouse in lieu of individual pieces.
Off-site Construction in Action – Case Study of Memorial Health System's Athens Medical Campus
NAC recently partnered with MODLOGIQ to design Memorial Health System's Athens Medical Campus in Athens, Ohio, a 100,000 square foot healthcare facility. Designed using modular off-site construction, the entire building was fabricated and assembled in a factory away from the project site. The exterior and interior building fabrication happened concurrently with the site excavation and foundation pouring. This process saved twelve months on construction and enabled the facility to open earlier than traditional on-site construction, generating revenue for the owner sooner.
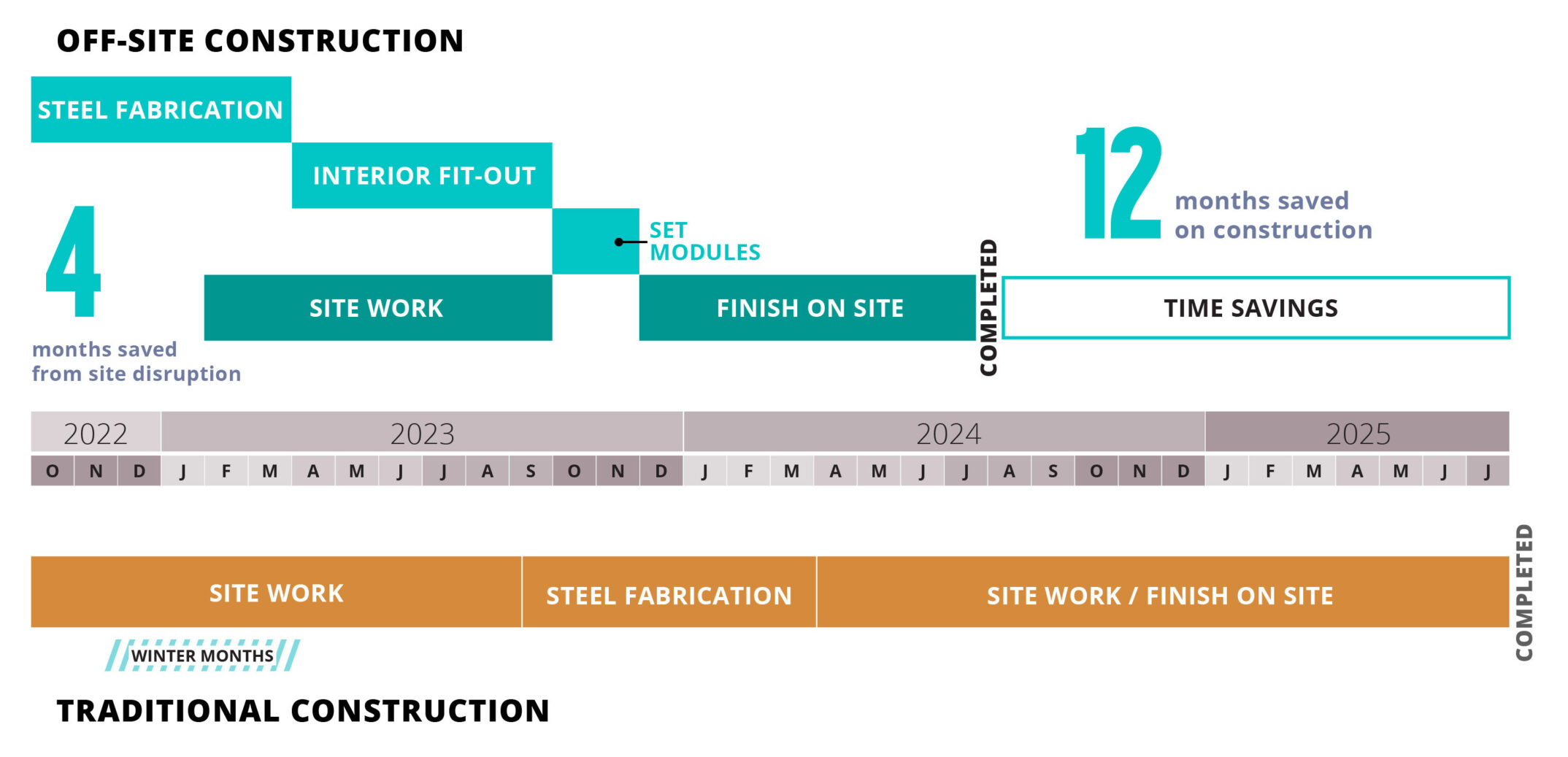
By using off-site construction, we were able to design complex spaces such as an Emergency Department, MRI, and Laboratory that would not be possible with a more traditional modular approach. On the MEP side, constructing the complete building off-site instead of using the modules approach allowed for installation of the complex systems needed to support an I2 Occupancy without risking misalignment of the systems once on site. When off-site fabrication was complete, a section of the MEP utilities was removed to ship the modules to their destination for reinstallation on-site.
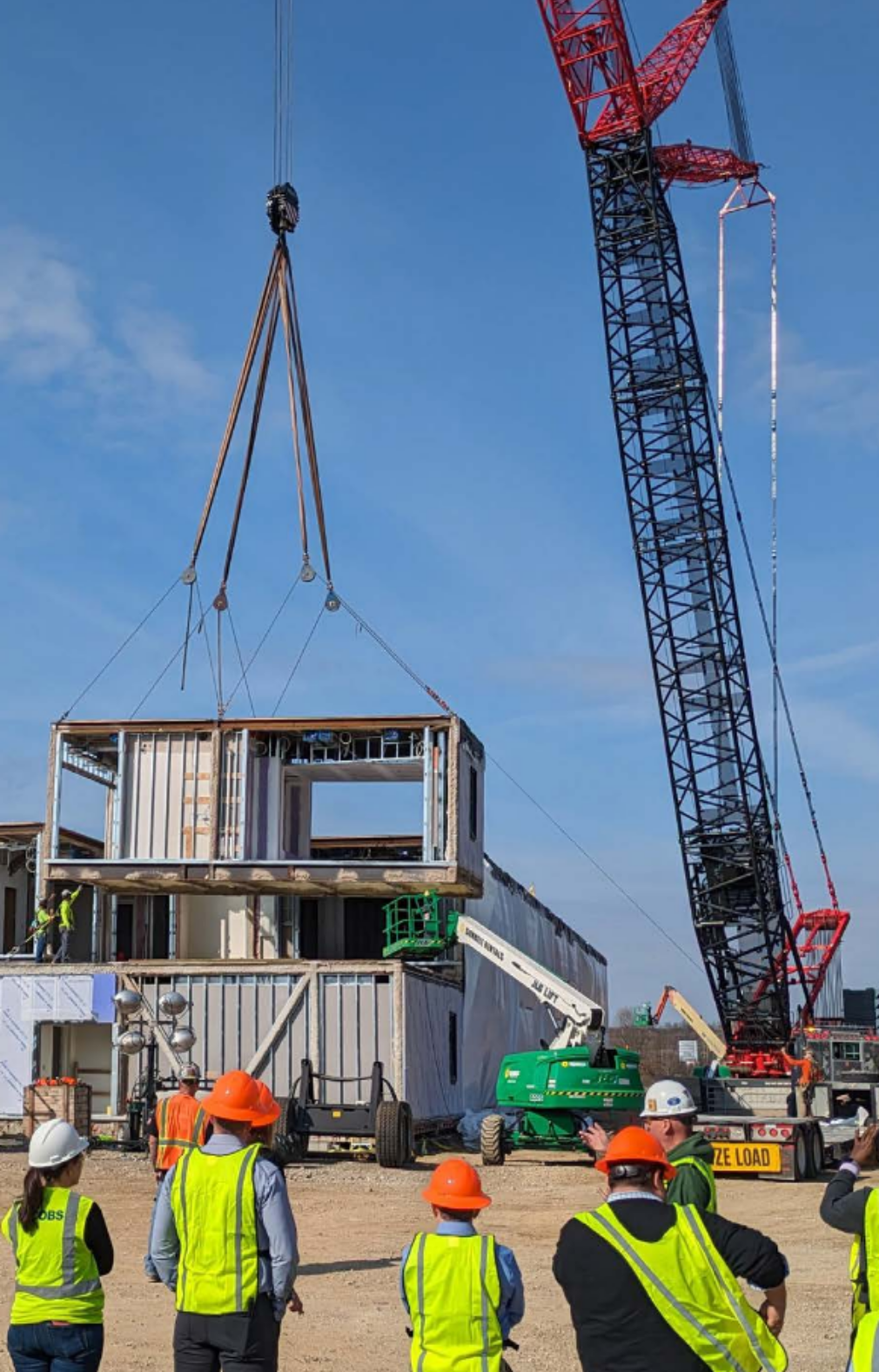
Example of the conduit at a module seam, fully installed then taken out and zip tied for transit.
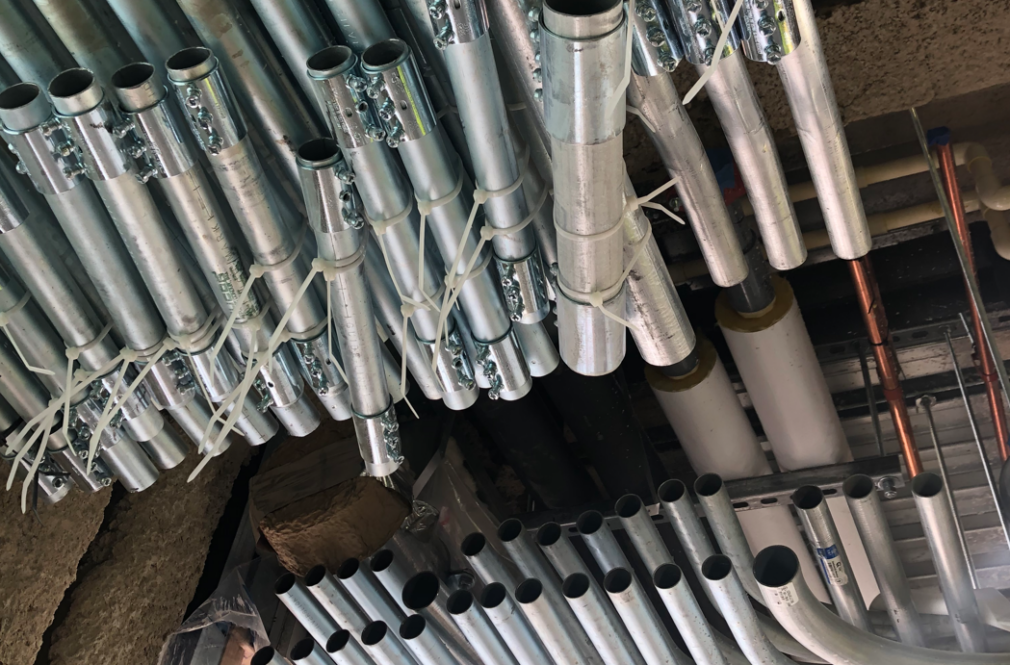
Example of the conduit at a module seam, fully installed then taken out and zip tied for transit.
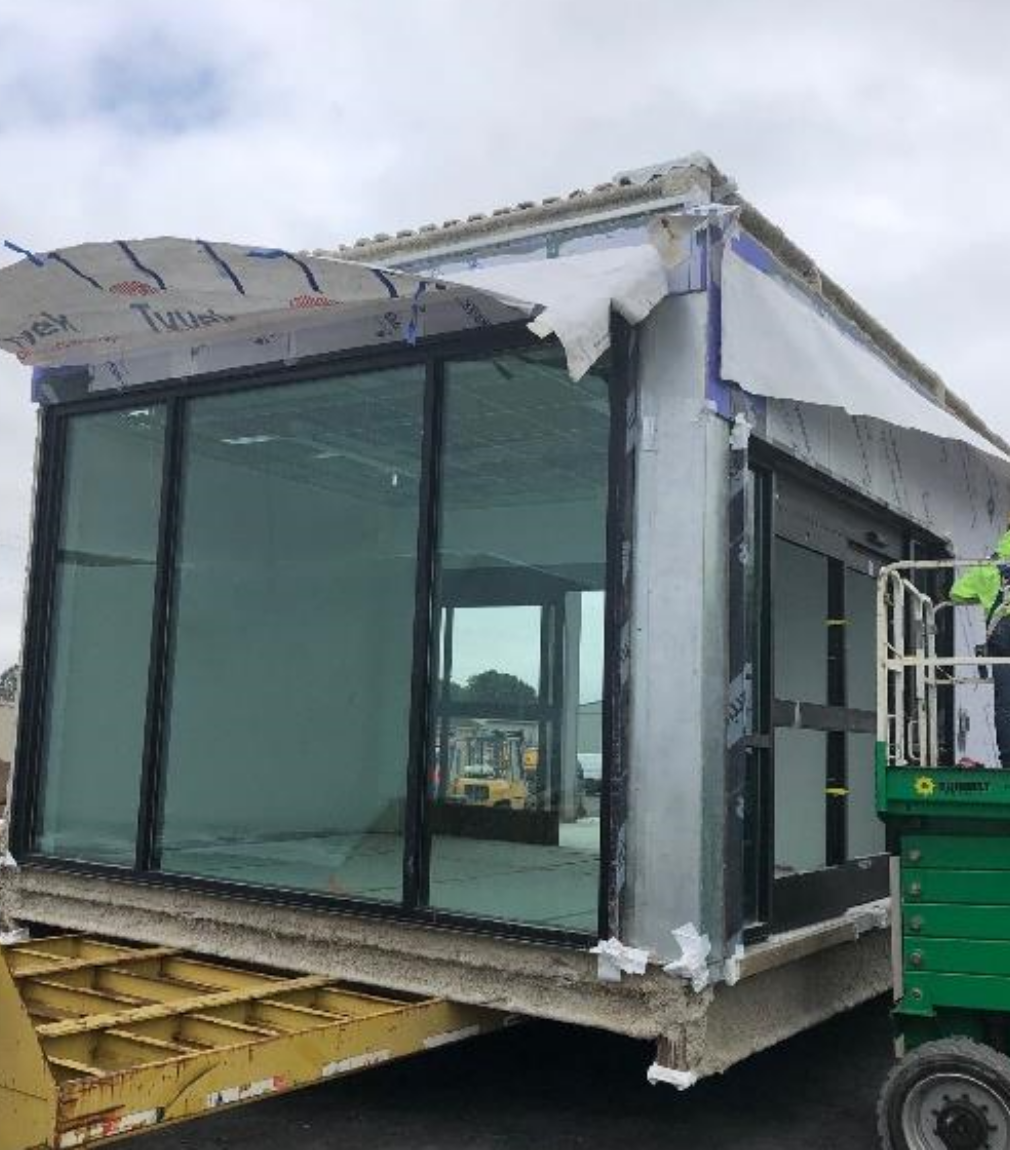
Module being prepared and loaded on truck bed for shipping to the site.
What does off-site construction mean for an owner, contractors, or the design team?
To answer this question, we look at some stories from the construction of the Athens Medical Campus.
Owner’s perspective:
Owners sometimes fear that with off-site construction they will be disappointed in the quality of construction. Yet, we have seen just the opposite. Recently, a Director of Facilities—looking at using off-site construction on a building with I2 Occupancy and the associated construction requirements that carries—attended a tour and was so impressed with the level of construction that he was excited to plan his next trip to the facility and move forward.
I2 Occupancy is achievable because of the customizable nature of off-site construction, supporting the complexities associated with fire ratings and healthcare program elements. In addition to customization, fabrication occurs in a controlled environment, with an adequate lay down area and all the MEP systems can be installed with reduced tolerances.
When a care team came to the factory for a mockup review, they had heard a lot of discussion about the unique off-site construction method being used. They were surprised to note that everything looked like a traditional construction site to them.
This is because it is traditional construction! Outside of the fact that modules will disassemble for shipping, the construction is like every other project with tighter tolerances. This is where the fully customizable approach of off-site construction comes in.
Takeaway: Having the owner team tour the off-site facility is an essential part of communicating the construction process to the full team. This step allows owner team members to better understand their building’s progress and communicate that internally and to their stakeholders.
Contractor’s perspective:
Before the modules arrive on site, the foundations must be surveyed, and since the building fabrication has already begun, the foundations need to be poured very precisely within a +0, -1/2” range.
This is beyond normal tolerances for the construction of concrete piers. A skilled team is required that works closely with the project team to build the modules off-site. In traditional construction, these tolerances are modified by the adjustment of steel and metal studs, until the final walls are all plumb. That approach cannot be done with off-site construction since it is already fabricated.
Takeaway: Consistent and clear communication between the design team, off-site construction team, and the on-site team is essential, so each knows the unique requirements of this delivery method.
Designer’s perspective:
As designers, off-site construction begins with embracing the columns.
Since the module size is limited, there are more columns to work with when laying out and designing the interior spaces. The number of columns should be seen as just another variable to work with.
Healthcare design has set size requirements that work with grids that can be replicated in modular construction. Experience with modular construction reveals patterns that guide modular size and how to plan program adjacencies both adjacently and vertically to make the building as efficient as possible.
Takeaway: Designing for off-site construction requires a shift in mindset. Rather than viewing columns as problems, they should be seen as design variables that can guide efficient space planning. Understanding and working with these patterns—grid sizes and program adjacencies—can lead to more effective and efficient building designs.
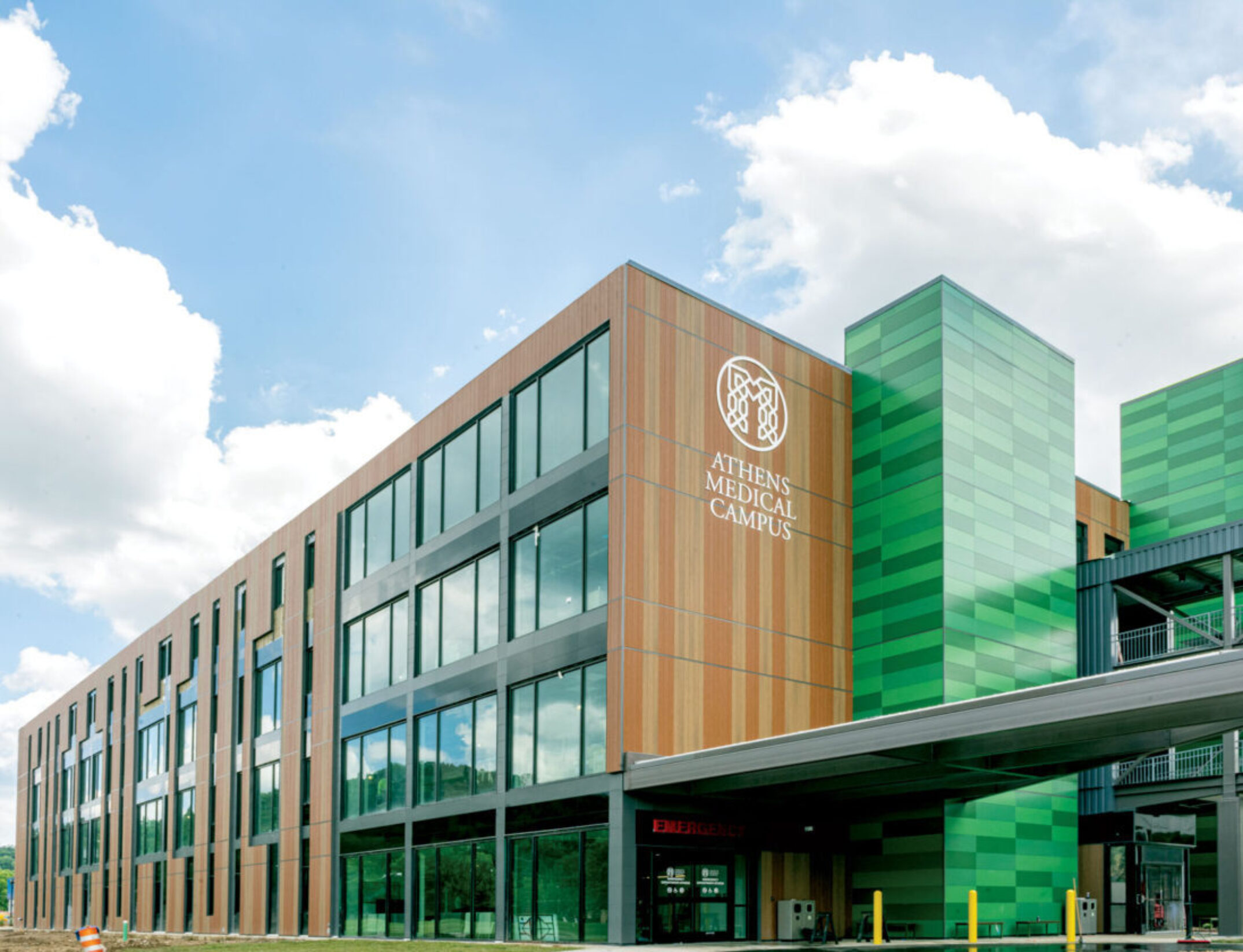
Modular construction encompasses a wide range of techniques and applications for healthcare, each with its own set of advantages. Understanding the nuances between these methods—whether it's the repetition of standardized units or the full customization possible with off-site construction—can empower project teams to make informed decisions. By choosing the appropriate modular approach, building owners can achieve their goals more efficiently, whether that means reducing costs, enhancing quality, or accelerating project timelines.
Look for our next article, where we’ll do a deep dive into why off-site construction works so effectively for healthcare projects.